Avoiding Pneumatic Malpractice
- Compressed Air Consultants, Inc
- Apr 29, 2023
- 4 min read
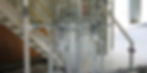
Problem
A cement import terminal had a multitude of problems that were causing production interruptions and environmental releases of dust due to poor air quality and low air pressure. The local com-pressor company diagnosed it as inadequate volume, drying and piping and recommended that all three be upgraded to the tune of $50,000. This would have in-creased the operating costs.
Solution
An audit of the entire system by an independent consulting firm specializing in compressed air found a very different root cause that cost no capital money to fix. The same audit found an oppor-tunity to reduce the operating costs (rather than increasing it) by 46% with a 22 month payback. The plant chose to go for the ROI route and the savings were realized while air pressure and quality issues were eliminated.
Plant Size Doesn’t Matter when it Comes to Cost Reduction and Avoidance
Do you think that your air system is so small that the potential operating cost reductions just aren’t there to justify a detailed audit by a compressed air expert that doesn’t sell compressors? As the technical training of compressor salespersons has been dumbed down in the past twenty years while the use of “automated surveys” has increased, the quality of recommendations has dropped off with serious financial consequences to the small and mid-sized plants.
The truth might surprise you. In most systems at small and mid-sized plants:
Project paybacks are no different than they are for large plants.
The cost of the audit is proportionately smaller than large systems.
And most importantly, the independent audit almost always finds greater opportunity or accomplishes the same goals for less capital as a compressor company audit.
A cement import terminal had typical productivity problems associated with air pressure and air quality problems including fugitive dust emissions, shortened bag life, poor valve performance, formation of small boulders in their silos, and so on.
Attempting to solve the problem in the compressor room, the local compressor company recommended adding new compressors, a desiccant dryer, and re-piping the air to the top of the silo at a cost of $50,000 however, this would have in-creased the operating costs by tens of thousands of dollars as well.

The primary dust collector was fed this wet air which caused the bags to blind. This led to dusting problems that affected the plant’s neighbors. The dust collector operator, not understanding why the air was wet, increased the duration and decreased the interval on the pulses. This increased the demand from roughly 25 CFM to roughly 150 CFM. This operation continued while the 75 horsepower was fixed. Once repaired, the plant attempted to shut the 125 horsepower off, but the plant air pressure dropped immediately. What the plant didn’t realize was that the new settings on the dust collector increased the demand to the level where the 75 horsepower could not keep up.
While the original $50,000 proposed project would solve the pressure problem, operating costs would have increased. The consultant’s solution had a very different price tag and a very different operating cost. If the pressure problem was the only problem they wanted to solve, the solution was limited to changing out the bags, re-set the dust collector controls while closing the valve from the bagging system compressor, all of which would have cost less than $1000 out of the maintenance budget.
The Audit
The first step in the audit was to define and de-scribe the system and begin the data collection process. Pressure, temperature and power data was collected for a week and as the system pro-file developed, some very striking issues emerged quickly as the root cause emerged.
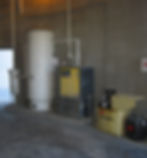
At some point in the past, the 75-horsepower primary compressor failed, and the plant elected to make an emergency connection to the 125-horsepower compressor system during the repair period. That emergency connection was made upstream of the 125-horsepower compressor’s dryer which meant that the air feeding the rest of the facility was wet.
The primary dust collector was fed this wet air which caused the bags to blind. This led to dust-ing problems with the plant’s neighbors. The dust collector operator, not knowing what was going on, increased the duration and decreased the interval on the pulses. This increased the demand from roughly 25 CFM to roughly 150 CFM. This operation continued while the 75 horsepower was fixed. Once repaired, the plant attempt-ed to shut the 125 horsepower off but the plant air pressure dove. What the plant didn’t realize was that the new settings on the dust collector increased the demand to the level where the 75 horsepower could not keep up.
So, while the original $50,000 proposed project would solve the pressure problem, operating costs would have increased. The consultant's solution had a very different price tag and a very different operating cost. If the pressure problem was the only thing they wanted to solve, all they needed to do was to change out the bags and reset the dust collector controls while closing the valve from the bagging system compressor, all of which would have cost $1,000 or so.
The consultant however found enough inefficiencies in the system that a whole new project was developed which provided the following:
A $32,000 per year operating cost reduction (46% total operating costs)
Air pressure stabilization throughout the facility
Air quality improvement throughout the facility
The plant could back up the primary system with the bagging system and all that was re-quired was a tie in that was after the dryer rather than before.
The project cost roughly the same as the compressor company project at $60,000 providing a 22-month payback.
The audit also found that the exhaust system for the bagging system compressor was inadequate which would lead to high temperature operation and premature lubricant failure. In addition, since the bagging system compressor was now required only 8 hours per week vs 120 hours (93% reduction), the maintenance requirements on this compressor would also be drastically reduced while increasing the overall lifetime of the machine. Overall maintenance costs would be further reduced since dust collector bag life would increase.
Summary - Lessons Learned
Smaller systems can have returns from air system projects that are just as good as those on larger systems.
Precise demand side work is often required to achieve the significant results.
Investigation is required prior to the audit to determine if a project is likely which also facilitates the unique scope of work suitable to a specific plant.
Looking at all financial impacts in a project make it that much more desirable whether it is operating costs, capital avoidance, or productivity gains.